Zirconia Fused Alumina
Your Trusted Source for Zirconia Fused Alumina
Great Abrasive is your go-to source for premium Zirconia Fused Alumina, designed to excel in diverse applications.
The perfect amalgamation of aluminum oxide and zirconium oxide brings the sharpness and durability of zirconia alumina to an ultimate equilibrium. We possess multiple patents in zirconia alumina cooling technology, enabling a rapid cooling of the solution from 2700 degrees to 1400 degrees within 5 seconds. This process yields an extremely fine crystalline structure, with sizes as small as 12 micrometers, thereby significantly enhancing the abrasion resistance of zirconia alumina.
Choose from a wide array of sizes tailored for your specific needs: from F6-F220 to P12-P220.
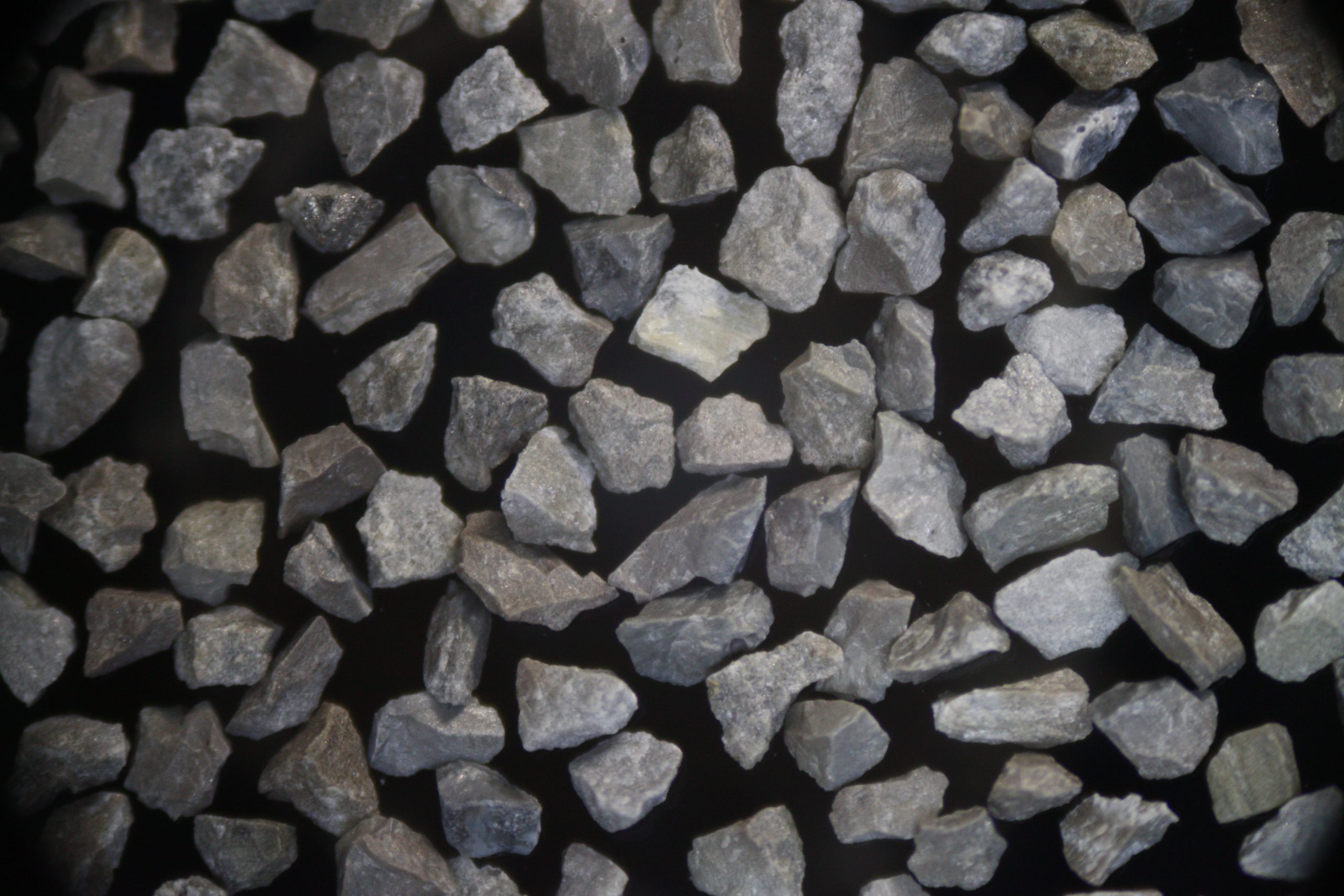
Zirconia Fused Alumina 25%
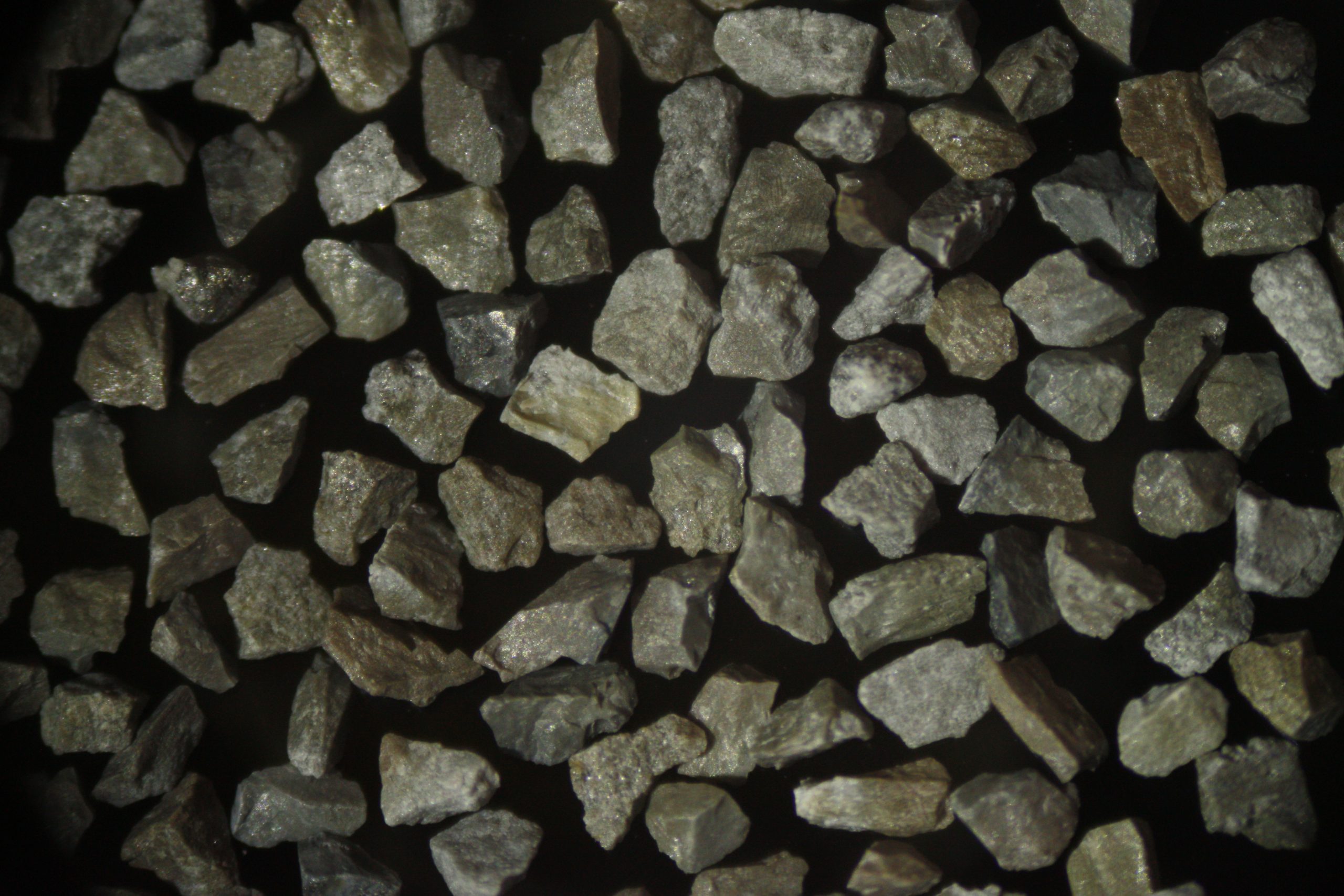
Zirconia Fused Alumina 40%
Excellence in Abrasives: Leading with Zirconia Alumina
Our Zirconia Alumina excels in supply robustness, unmatched quality, and tailored solutions, establishing us as a top choice for premium brands. With a substantial annual production and a versatile product lineup, we precisely fulfill your unique requirements with unparalleled excellence.
- Robust Production, Reliable Supply
Our three furnaces ensure a premium Zirconia Fused Alumina output of 8,000 tons annually, reinforcing your supply chain with unmatched dependability.
- Quality That Competes with Giants
Our Zirconia Fused Alumina rivals the quality of industry giants Saint-Gobain and Imery, ensuring your products are made with materials that meet the highest standards of excellence. Choose us to elevate your offerings. - Preferred by Top Brands
Renowned for our exceptional product quality and value, leading brands like Tyrolit, Deerfus, and NCA choose us as their primary supplier.
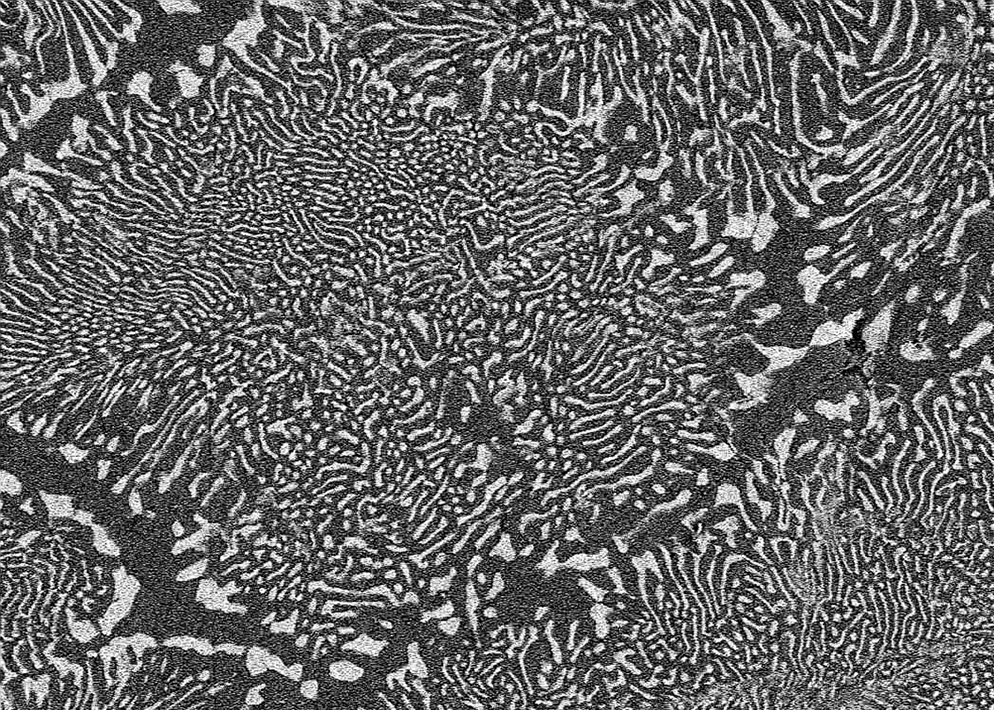
- Innovation at Its Core
Our R&D prowess shines with multiple patents in Zirconia Alumina technology and exclusive advancements in grinding and mixing equipment, ensuring we lead in innovation. - Diverse Product Range
Our Zirconia Fused Alumina, in 25% and 40% options, suits every need. Ideal for bonded abrasives (F6-F220) and coated versions (P12-P220), it offers the flexibility of standard to premium grades for any application. - Custom Solutions for Precise Needs
Our expertise lies in tailoring products to your exact specifications, from chemical compositions, PSD, grain shapes to surface treatments. We ensure unparalleled precision to meet your unique demands efficiently.
Why Choose Zirconia Fused Alumina from GREAT Abrasive?
Opt for GREAT Abrasive for its unmatched expertise, guaranteed quality, flexible ordering, commitment to customer satisfaction, and efficient processes. Our dedication to excellence and integrity in service ensures that we not only meet your expectations but exceed them, making us the go-to provider for Zirconia Alumina.
Unmatched Expertise
Leveraging three decades of dedicated Zirconia Alumina production, GREAT Abrasive is your trusted ally, ensuring project success with unmatched expertise and commitment.
Guaranteed Excellence
With advanced testing and strict quality control, we guarantee consistently premium Zirconia Alumina, redefining excellence.
Beyond Sales Support
Enjoy peace of mind with every order through our post-purchase integrity-first approach, ensuring quality and logistic assurance.
Flexibility for All Orders
No-minimum order policy accommodates any project size, offering unparalleled flexibility and convenience.
Sample the Best
Test our Zirconia Alumina through free samples and understand why we're the chosen partner for industry leaders.
Effortless Procurement
Streamlines your buying experience, ensuring a smooth process so you can concentrate on your priorities.
FAQ About Zirconia Fused Alumina
Zirconia Fused Alumina (ZFA) is a type of alumina that is fused with zirconia in a high-temperature electric arc furnace, creating a highly durable and tough abrasive material.
It is known for its high toughness, excellent wear resistance, good thermal stability, and resistance to corrosion, making it superior for abrasive and refractory applications.
ZFA has a higher toughness and wear resistance compared to regular Alumina due to the addition of zirconia, which enhances its physical properties.
It is widely used in the production of abrasive tools, such as grinding wheels and sandpapers, refractory materials, ceramic parts, and in surface preparation and finishing processes.
Yes, its high toughness and cutting efficiency make it suitable for use in waterjet cutting applications, providing precise and efficient cutting.
ZFA is available in a wide range of grit sizes, from coarse particles for heavy-duty grinding to fine particles for precision finishing.
Absolutely, its high toughness and ability to resist thermal shock make it ideal for cutting, grinding, and polishing stainless steel without causing surface contamination.
Initially, it may be more expensive than some alternatives, but its durability and efficiency often lead to lower overall costs due to reduced replacement needs and downtime.
It should be stored in a dry, well-ventilated area away from moisture and temperature fluctuations to maintain its quality and performance characteristics.
Zirconia enhances the material's mechanical strength, thermal stability, and wear resistance, enabling it to perform better in aggressive grinding and cutting operations.
Tools made with ZFA typically have a longer lifespan due to their superior toughness and wear resistance, offering better cost-efficiency over time.
Yes, it is versatile and effective in both conditions, providing excellent results in dry grinding and showing remarkable performance in wet environments due to its low moisture absorption.
Proper protective equipment, such as gloves, goggles, and dust masks, should be used to handle and work with ZFA, minimizing the risk of skin irritation and inhalation of dust particles.
It is considered to have a low environmental impact when disposed of properly, though recycling and proper waste management practices are recommended to minimize its ecological footprint.
Its high melting point and thermal stability make it an excellent choice for refractory linings and components, resisting high temperatures and thermal shocks in industrial furnaces.
Yes, there are variations, including different zirconia contents and modifications aimed at enhancing specific properties for certain applications.
Have More Questions?
We are happy to answer any questions you may have about our products and company.
Zirconia Fused Alumina Buyer’s Guide
At Great Abrasive, we understand the challenges you encounter, and we stand ready to guide you in finding the perfect solution to fulfill your project’s unique demands. Let’s streamline the process and assist you in discovering the ideal Zirconia Fused Alumina that precisely match your specific requirements.
Table of contents
Chapter 1
What is Zirconia Fused Alumina?
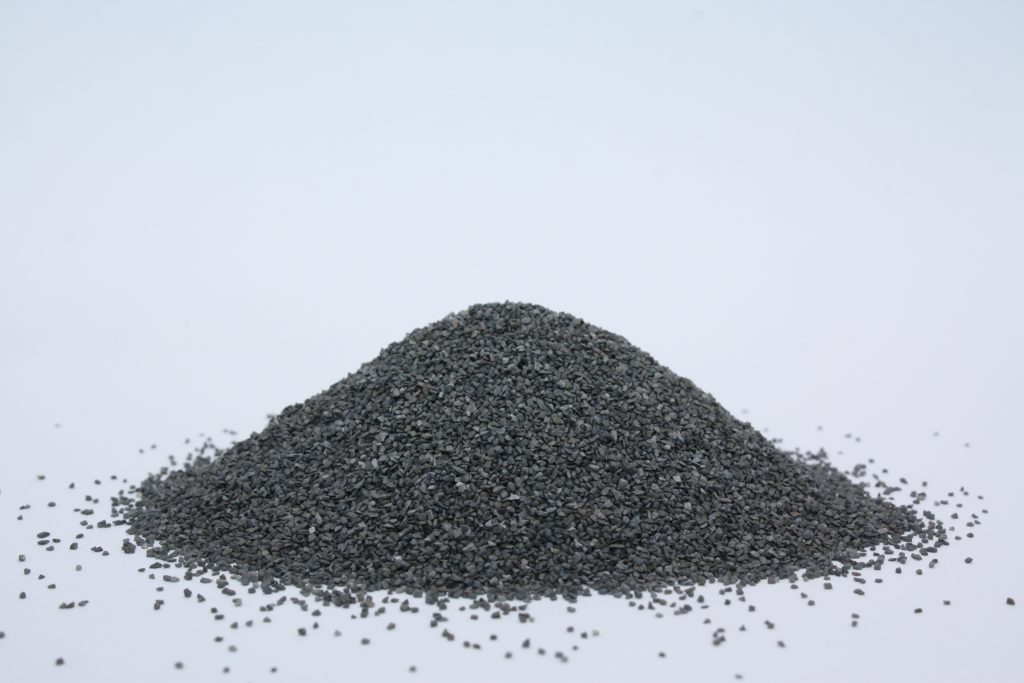
Zirconium Fused Alumina is a eutectic structure abrasive of Al2O3 and ZrO2. It is a very durable abrasive material obtained by using high-purity alumina and desiliconized zirconia as the main raw materials. It is melted at high temperature in an electric arc furnace and then rapidly cooled and crystallized. The material has a very fine and uniform microcrystalline structure, which provides high toughness while also ensuring good self-sharpening properties.
Chapter 2
Property of Zirconia Fused Alumina
Thermal Stability
One of the defining properties of ZFA is its excellent thermal stability. It can withstand high temperatures without losing its structural integrity or performance capabilities. This property makes it particularly valuable for applications that involve high-temperature processes, such as metal fabrication and foundry operations.
High Toughness
ZFA is tougher than standard alumina abrasives. This toughness translates to a higher resistance to fracture and wear, allowing it to maintain its effectiveness over longer periods, even under harsh grinding conditions. This durability reduces the need for frequent abrasive replacements, enhancing operational efficiency.
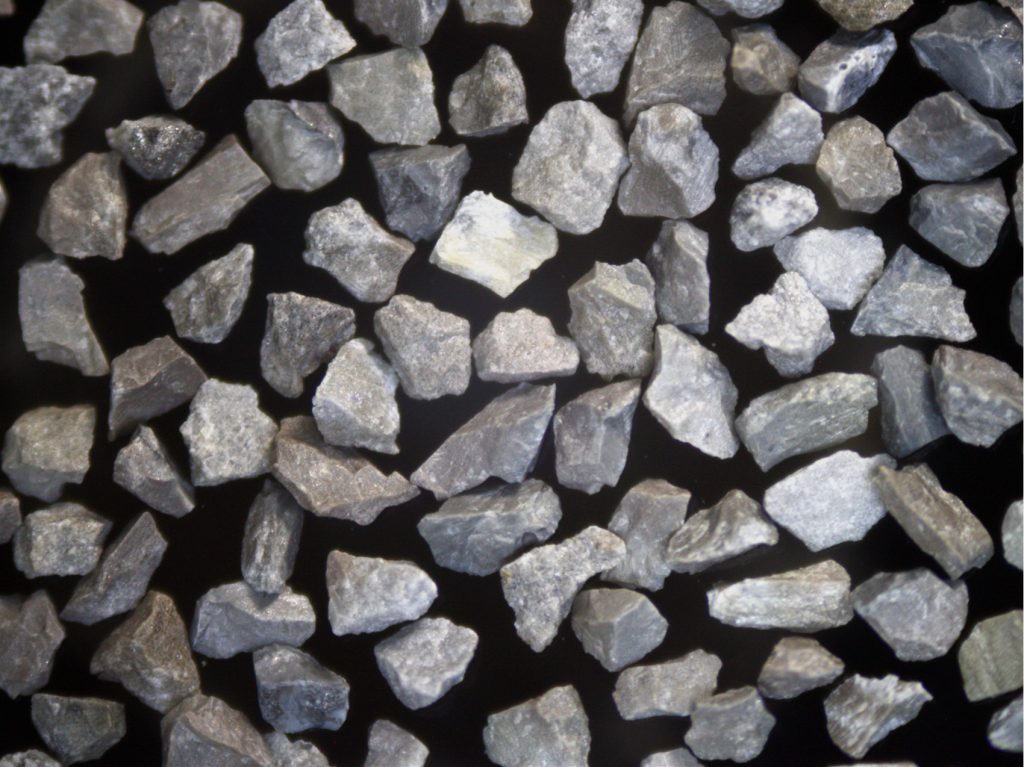
Chemical Inertness:
Zirconia Fused Alumina exhibits a high degree of chemical inertness, making it resistant to attack by most acids and alkalis at normal temperatures. This property ensures that it maintains its abrasive properties even in environments that would degrade lesser materials.
Low Thermal Expansion:
Compared to other abrasive materials, ZFA has a relatively low coefficient of thermal expansion. This characteristic minimizes the risk of dimensional changes in workpieces during high-temperature applications, ensuring more accurate and consistent results.
Aggressive Cutting Performance:
Due to its superior hardness and toughness, ZFA provides aggressive material removal rates. It cuts through hard materials more effectively than many other abrasives, making it ideal for heavy-duty grinding and cutting tasks.
These properties collectively make Zirconia Fused Alumina a material of choice for demanding abrasive applications, offering a combination of durability, efficiency, and versatility that is hard to match with other abrasive materials.
Chapter 3
Specification of Zirconia Fused Alumina
Chemical Analysis | |||
---|---|---|---|
Spec | ZAF25 | ZAF40 | |
Al2O3 | 68% Min | 56% Min | |
ZrO2 | 22-28% | 36-43% | |
SiO2 | 0.6% Max | ||
Fe2O3 | 0.5% Max | ||
TiO2 | 0.5% Max |
Physical Property | ||
---|---|---|
Spec | ZAF25 | ZAF40 |
Color | Grey | |
Crystal Structure | Eutectic α-Al2O3 | |
Crystal Size | 15-20 um | 10-15 um |
Melting Point | 1950℃ | 1900℃ |
Microhardness | 1950 kg/mm2 | 1650 kg/mm2 |
True Density | 4.3 g/cm3 | 4.6 g/cm3 |
Magnetic objects | 0.015% Max |
Chapter 4
How is Zirconia Fused Alumina produced?
Are you curious about Zirconia Fused Alumina is produced? Here I will give you a simple decryption.
The production of Zirconia Fused Alumina involves selecting top-quality raw materials, precise mixing, and tightly controlled smelting, highlighted by a rapid cooling technology that significantly reduces temperatures to achieve a fine crystal structure. The process concludes with careful selection, crushing, purification, and stringent quality checks before packaging, ensuring a premium abrasive product.
- Control of Raw Material Purchasing
Quality checks and supplier audits ensure only the best raw materials are used.
- Mixture Control Before Smelting
Precise calculation and uniform mixing of raw materials based on chemical analysis.
- Control of Smelting Process
The smelting process is strictly regulated, from maintaining the material proportions to monitoring the smelting liquid’s quality and furnace conditions. The process emphasizes temperature and level control, alongside careful observation of the smelting liquid’s color and sound, to determine the optimal release time.
- Cooling
The most significant difference in the production process of Zirconia Fused Alumina compared to regular alumina lies in its unique cooling technology. Our company’s patented rapid cooling device for Zirconia Fused Alumina smelting can reduce the temperature of the molten material from 2700 degrees to below 1400 degrees in just 5 seconds. This rapid cooling is a crucial factor in achieving the extremely fine crystal size of Zirconia Fused Alumina.
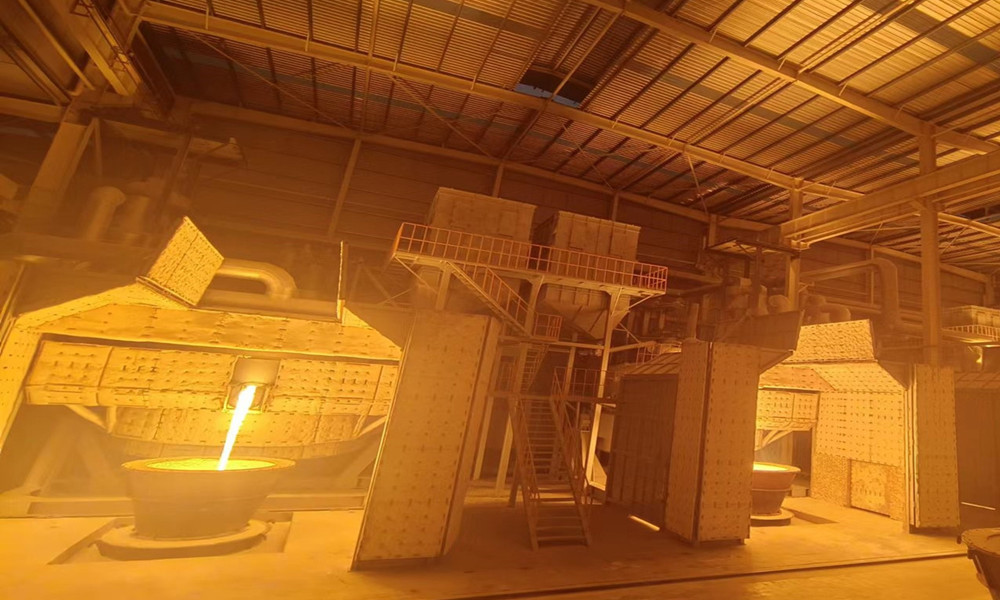
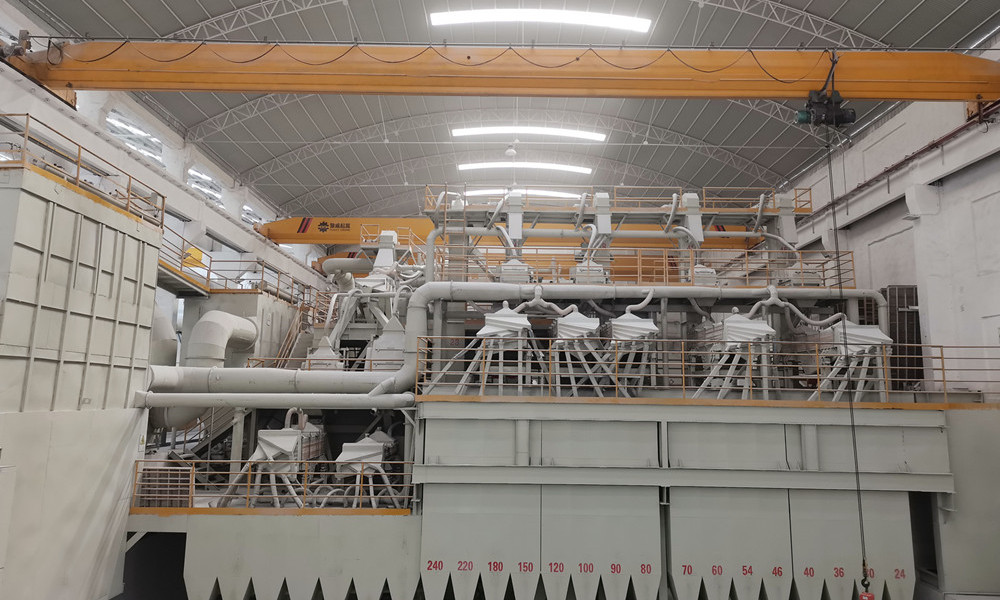
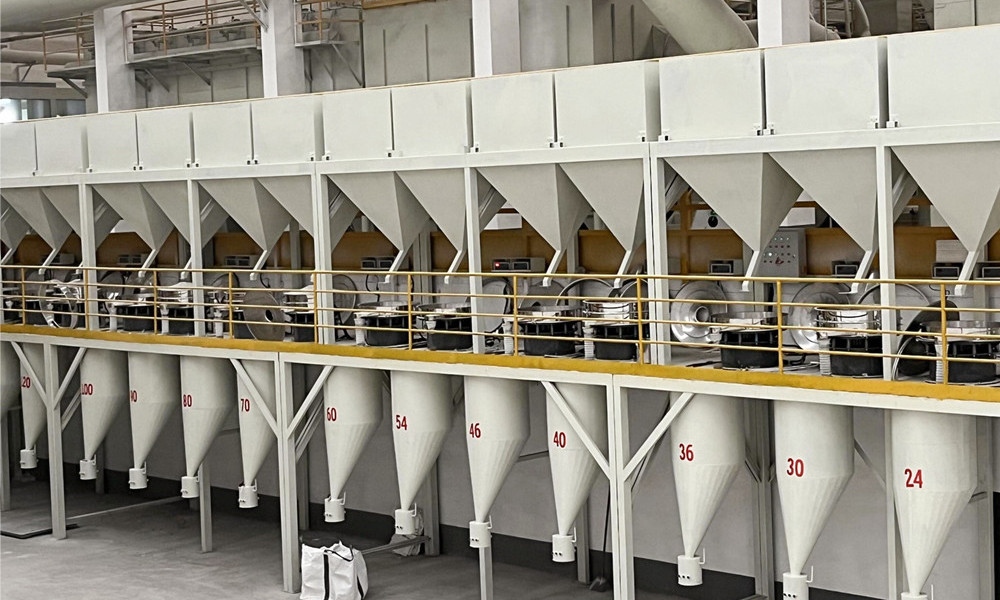
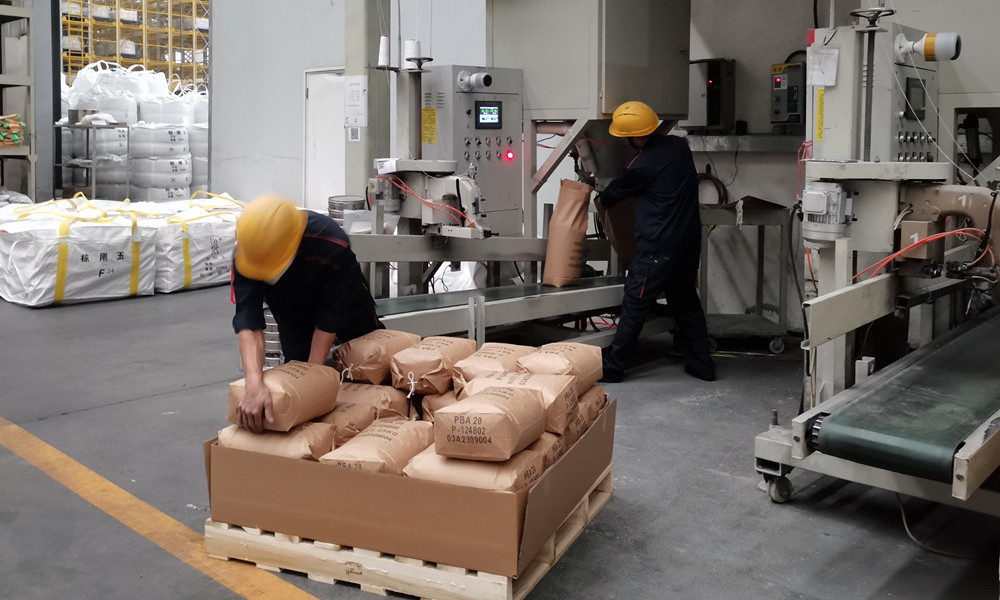
- Selecting Control of Smelting pieces
Selecting smelting pieces involves manual selection of those under 7mm thick after over 10 hours in cooling packs, with QC approval required before proceeding to ensure only qualified pieces are used, separated from unqualified ones and oxidation layers.
- Crushing
Once cooled, the blocks are crushed into smaller pieces. This process is crucial for breaking down the material into manageable sizes for further processing and for creating a range of grain sizes suited to different applications.
- Magnetic Separation
This step involves the removal of any magnetic contaminants to ensure the purity of the Zirconia Fused Alumina.
- Washing and Drying
The crushed Zirconia Fused Alumina is then washed to remove any impurities. After washing, the material is dried to eliminate moisture. - Control of Sieving & Packaging
The final quality control checks on grain size distribution before the product is packaged for market.
In conclusion, the production of Zirconia Fused Alumina at our facility is a testament to our commitment to quality and innovation, delivering an abrasive product that stands unparalleled in performance and reliability.
Chapter 5
What is Zirconia Fused Alumina Used For?
Zirconia Fused Alumina is a high-performance abrasive material known for its toughness and durability, making it ideal for a wide range of applications, particularly in industries that demand high precision and efficiency. Its key uses include:
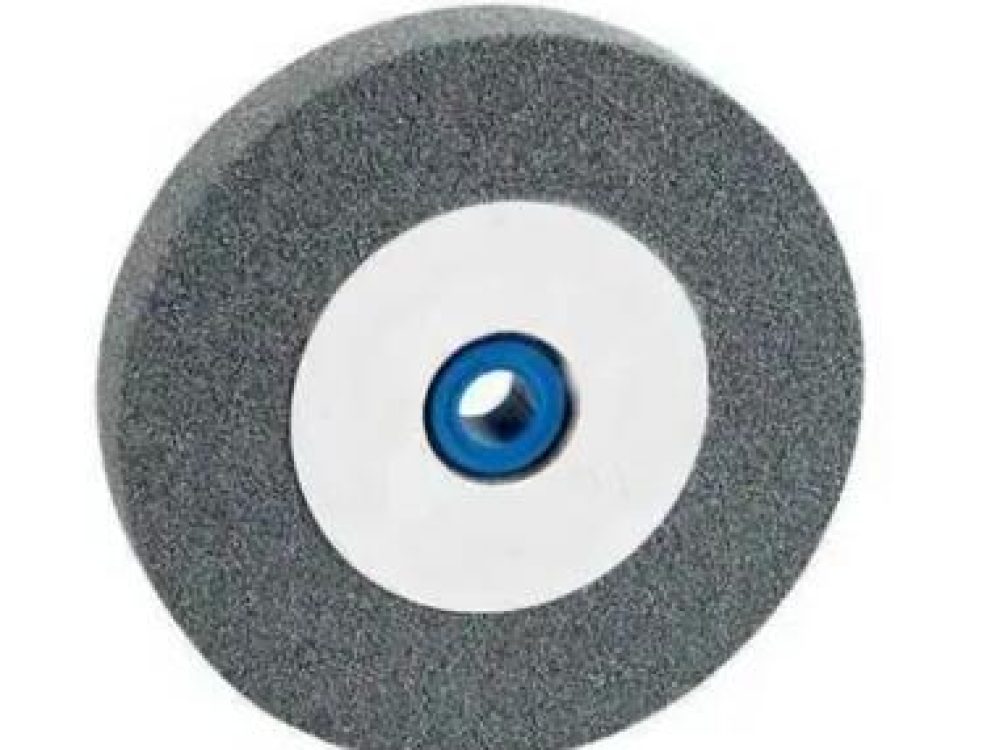
Abrasive Tools
It’s extensively used in the manufacturing of grinding wheels, sandpaper, and abrasive belts. Due to its high toughness, it’s particularly suited for heavy-duty grinding, cutting, and sanding applications.

Refractory Materials
Thanks to its high temperature resistance, Zirconia Fused Alumina is used in the production of refractory bricks and shapes, as well as monolithic refractories. These materials are essential for high-temperature processes in industries like steel, glass, and cement manufacturing
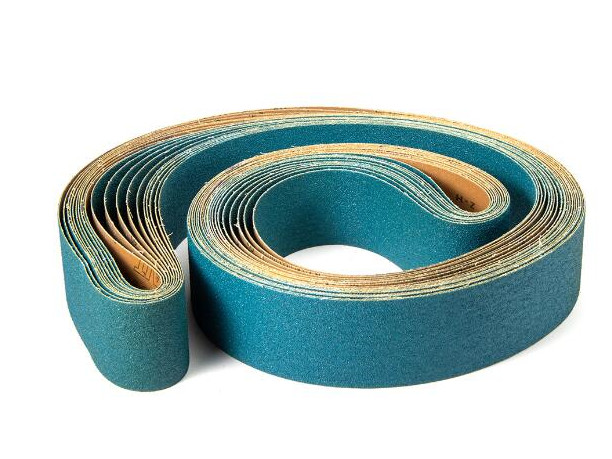
Coated Abrasives
It is employed in coated abrasive products like discs, sheets, and rolls used for finishing and polishing in the metalworking, woodworking, and automotive sectors.

Surface Preparation
Zirconia Fused Alumina is utilized in surface preparation processes, including blasting and cleaning of metal surfaces, to remove rust, scale, and other contaminants, preparing surfaces for coating or painting.
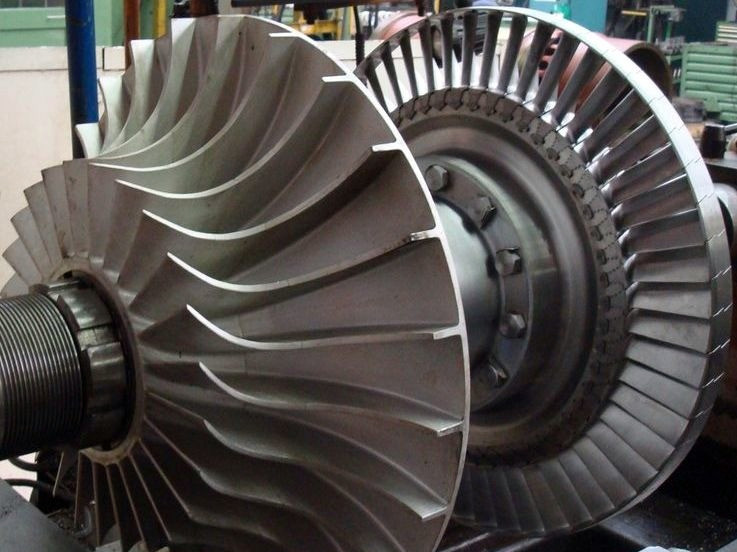
Investment Casting
It’s used in the shell building process of investment casting to improve the shell’s strength and resistance to high temperatures, enabling the production of precision metal parts with complex shapes.
This diversity in applications highlights the versatility and importance of Zirconia Fused Alumina in various industrial processes, offering solutions that require abrasion resistance, durability, and thermal stability.
Chapter 6
When comparing Zirconia Fused Alumina 25% (ZAF25) and Zirconia Fused Alumina 40% (ZAF40), the key differences hinge on zirconia content, impacting their performance and applications:
Item | ZAF25 | ZAF40 |
---|---|---|
Zirconia Content | 25% | 40% |
Wear Resistance | Moderate | High |
Toughness | Good | Excellent |
Thermal Stability | Moderate | High |
Cost | More cost-effective | Higher, reflecting superior properties |
Application | Suitable for general metal grinding, especially when a higher cutting rate is required rather than extreme abrasiveness. | Particularly suitable for demanding grinding tasks, such as processing aerospace components, or where extreme wear resistance and thermal stability are required. |
The choice between ZAF25 and ZAF40 should be guided by the specific requirements of the application, balancing the need for performance with budget constraints.
Zirconia Fused Alumina 25% vs. Zirconia Fused Alumina 40%
Chapter 7
Key Considerations When Buying Zirconia Fused Alumina
When purchasing Zirconia Fused Alumina, several key considerations ensure you select the right product for your specific needs, optimizing performance, cost-effectiveness, and efficiency. Here are the critical factors to consider:
Purity and Composition:
Check the purity level and chemical composition of the Zirconia Fused Alumina to ensure it meets your application’s requirements. The presence of certain impurities or variations in composition can significantly affect performance.
Grain Size and Distribution:
The grain size and its distribution (Particle Size Distribution, PSD) are crucial for the performance of abrasive tools. Different applications require different grain sizes, from coarse grains for heavy-duty grinding to fine grains for precision finishing.
Toughness and Hardness:
The toughness and hardness of the material determine its durability and cutting efficiency. Ensure these properties align with your application needs to prevent premature wear or failure.
Regulatory Compliance:
Verify that the Zirconia Fused Alumina meets all relevant environmental and safety regulations, especially if you’re operating in or supplying to markets with strict regulatory standards.
Thermal Stability:
For applications involving high temperatures, such as refractory materials or investment casting, the thermal stability of Zirconia Fused Alumina is a vital consideration.
Bulk Density:
This affects the material’s performance in abrasive applications. A higher bulk density can indicate a more durable abrasive, which is essential for certain grinding or blasting operations.
Quality Control and Standards:
Ensure the supplier adheres to strict quality control measures and international standards. Consistency in quality is vital for predictable performance and product reliability.
Supplier's Reputation and Experience:
A supplier with a proven track record and experience in producing Zirconia Fused Alumina is more likely to provide high-quality materials and valuable technical support.
Cost-effectiveness:
While not compromising on quality, consider the total cost of ownership, including the price per unit, shipping, and potential for volume discounts. A slightly higher upfront cost for a superior product can result in lower overall expenses due to longer lifespan and reduced downtime.
Customization and Technical Support:
If your application requires specific characteristics, check if the supplier offers customization options and technical support to help you achieve optimal results with their product.

By carefully considering these factors, you can select a Zirconia Fused Alumina product that best suits your needs, contributing to the success and efficiency of your operations.
Chapter 8
Zirconia Fused Alumina Packaging and Transportation Tips
Purchasing Zirconia Fused Alumina necessitates careful packaging and transportation to maintain its quality. Here are streamlined tips for effectively handling Zirconia Fused Alumina:
Packaging Tips
- Moisture Barrier: Choose materials with excellent moisture resistance. Moisture-proof films or sealed bags are essential.
- Durability: Select strong, durable packaging to endure transportation pressures.
- Size Appropriateness: Ensure packaging is correctly sized for the volume, optimizing protection and efficiency.
- Pallet Corner Smoothing: Smooth pallet corners to prevent packaging damage.
- Strapping Protection: Use protective boards under straps to avoid bag damage.
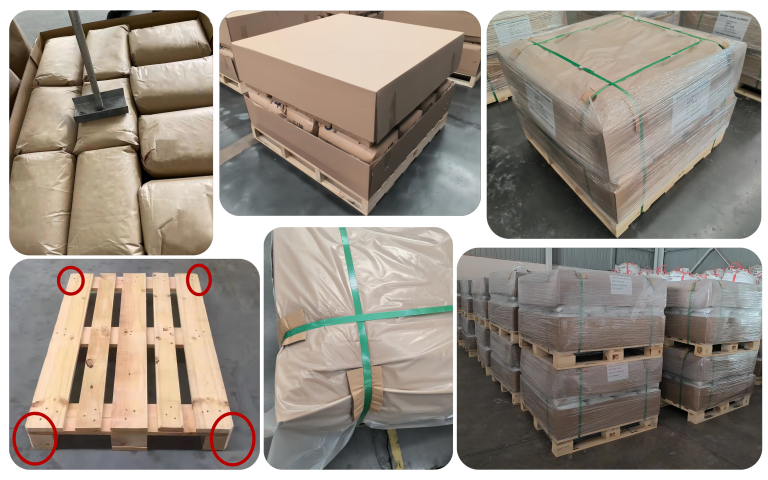
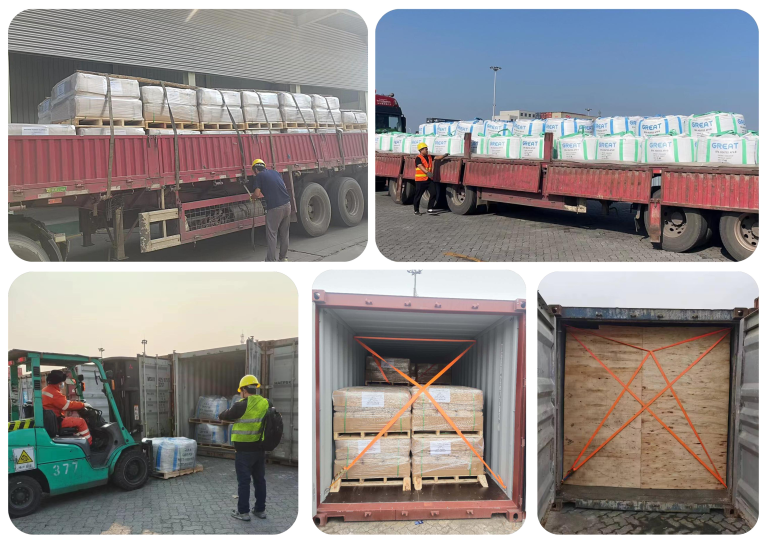
Transportation Tips
- Container Organization: Arrange packages neatly in containers to prevent damage.
- Transit Protection: Secure goods well for factory-to-port transit, protecting against road hazards.
- Mixed Loading Care: When combining pallets and bulk bags, use cushioning to reduce movement and prevent damage.
- Weather Prep: In humid or rainy weather, increase packaging’s moisture protection and consider container desiccants.
Efficient packaging and transportation are critical for preserving Zirconia Fused Alumina quality. By focusing on moisture prevention, packaging integrity, and careful transit handling, you can ensure your Zirconia Fused Alumina arrives in excellent condition. Partnering with a supplier knowledgeable in these areas is key to minimizing transit risks and maintaining product standards.
Chapter 9
In Summary
Selecting the right Zirconia Fused Alumina (ZFA) abrasives is key to achieving superior performance in various grinding and finishing tasks, from precise manufacturing endeavors to rigorous heavy-duty processing. Navigating the vast array of options might seem overwhelming, especially for those less experienced in the abrasive industry.
Introducing Great Abrasive, your trusted ally and foremost authority in the provision of Zirconia Fused Alumina abrasives. We are committed to excellence, offering elite Zirconia Fused Alumina products engineered to fulfill all your grinding, cutting, and finishing demands. With a rich history spanning over thirty years in the abrasive industry, Great Abrasive has the knowledge and skill to refine the selection process, delivering bespoke solutions that overcome your specific operational hurdles.
Choose Great Abrasive for premier Zirconia Fused Alumina abrasives, and let us assist you in unraveling the complexities of abrasive technology. Our dedication guarantees you attain the optimal surface treatment results, propelling your projects to success with our unparalleled support.
Elevate Your Cutting and Grinding with Our Zirconia Fused Alumina!
Discover the unmatched durability and cutting efficiency of Zirconia Fused Alumina from GREAT Abrasive. Tailored for your unique applications, it’s the choice for those demanding the best in toughness and longevity for their heavy-duty grinding and cutting operations.
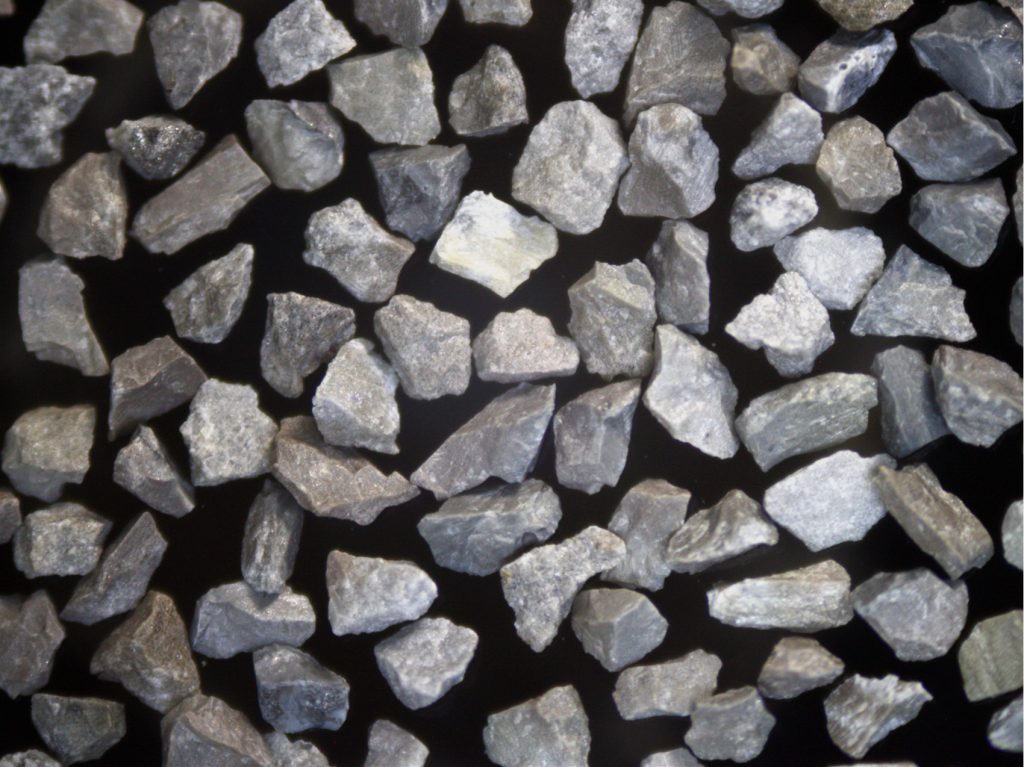
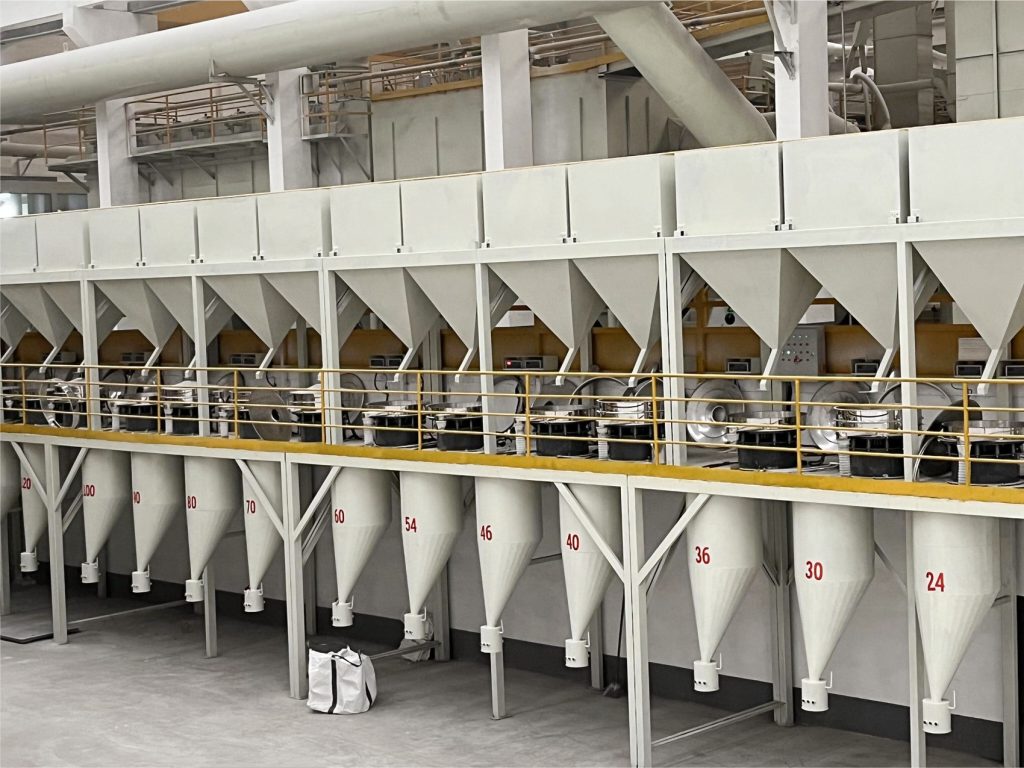
