Curious about the journey of pink fused alumina and how it plays a crucial role in high-quality abrasives? Let’s delve into the detailed production journey of this indispensable industrial gem, which finds extensive use in the manufacturing of grinding wheels and abrasive tools. From sourcing top-grade raw materials to the rigorous refining process, I’ll guide you through every meticulous step.
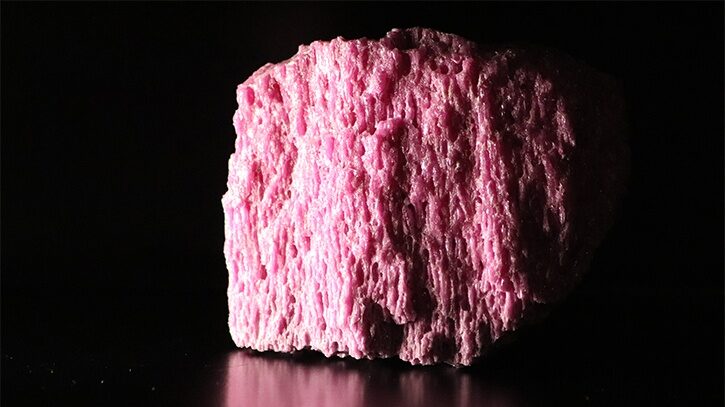
The Raw Material Stage
For pink fused alumina, the essential ingredients are high-purity aluminum oxide and a controlled amount of chromium oxide. The precise amount of chromium determines whether the final product will be of low, medium, or high chromium content. This unique combination gives the abrasive its distinctive pink hue and ensures exceptional durability and toughness.
The raw materials are melted in a fixed electric arc furnace at over 2000°C for about 25 hours. This intense heat allows the raw materials to fuse together, creating a molten blend that can be molded into blocks. Once cooled, the mixture is sorted by hand to select the highest-quality blocks for further processing.
The aluminum oxide used is crucial to the quality of the final product, influencing its hardness and thermal properties. The addition of chromium oxide imparts toughness and a characteristic pink color. Proper blending of these components during melting ensures the right composition and structure for the final product.
Crushing, Shaping, and Screening
After selecting the best blocks from the furnace, the next step is to break them down into usable sizes. The material is first crushed using jaw crushers, then shaped by rollers to achieve the desired particle size distribution. Magnetic separation is also employed at this stage to remove any ferrous contaminants from the final product.
The material is then screened into various sizes based on international standard sizes, ranging from F4 to F220. This step is critical because the grain size will significantly impact the quality of the final abrasive product. Larger grains are used for coarse grinding, while finer grains are suitable for finishing applications.
We use precision sieving equipment to ensure that the final product meets the exact specifications required by our customers. Maintaining consistency in the grain size distribution is essential to ensure that the abrasive performs as expected in its intended application.
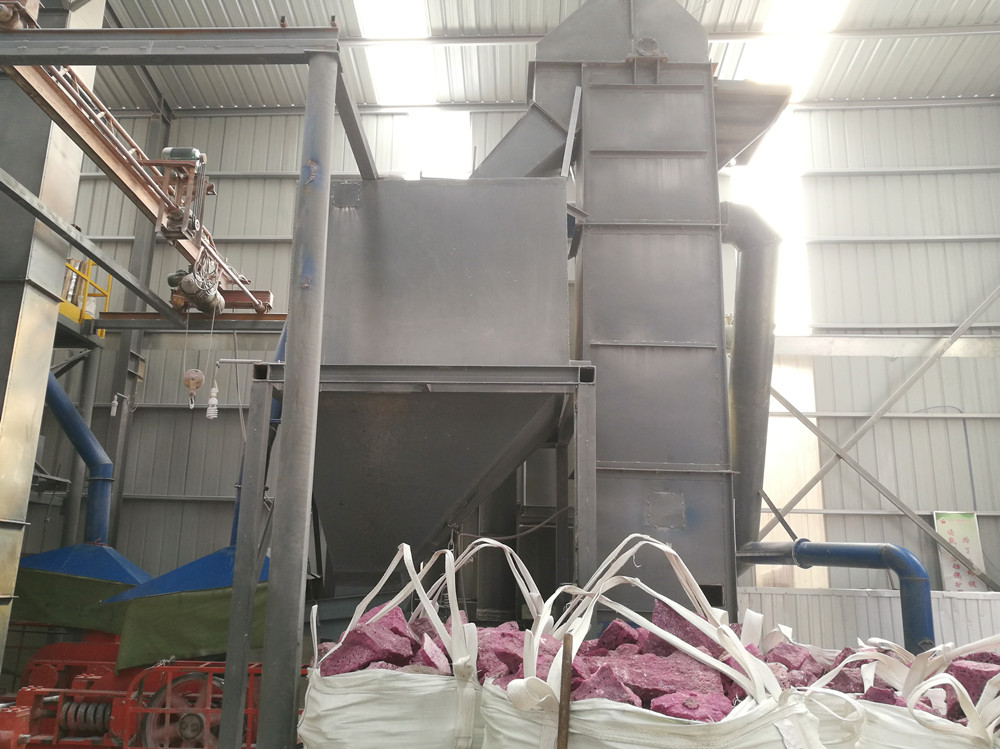
Micro-Powder Refinement
The next step involves refining the powder further to produce the fine particles required for specific abrasive applications. The fine powder undergoes acid and water washing to remove impurities, followed by the overflow process for precise grading. Microscopes and particle counters are used to monitor the grading process in real time, ensuring that the powder meets strict quality standards.
The refined product is then fed into sedimentation pools for drying. The dried material is sifted through ultrasonic vibrating screens to remove any remaining impurities and to achieve the desired particle size distribution.
This step is crucial because the fine powder must meet specific size requirements for applications like polishing and lapping. The powder’s quality will directly affect the finish and accuracy of the final product.
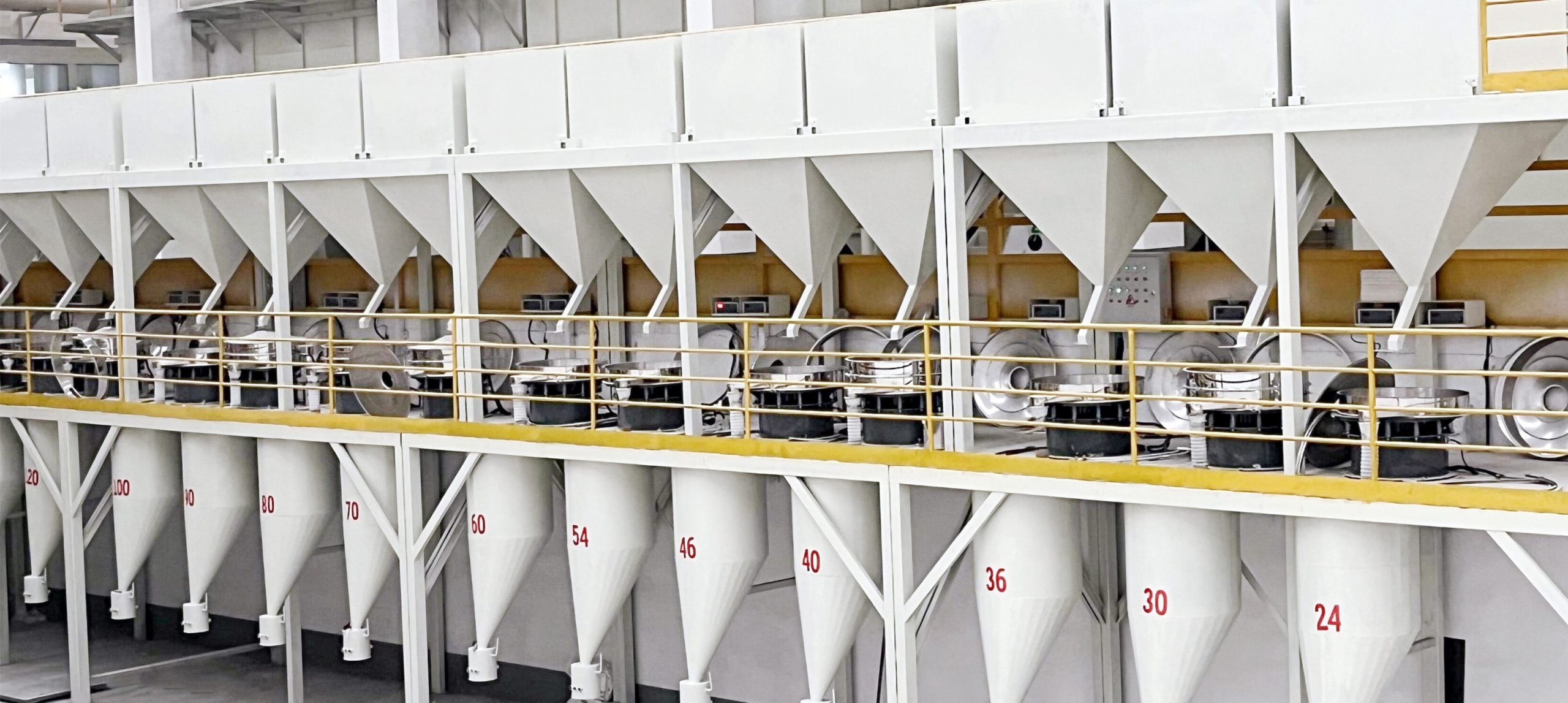
Production Considerations
Maintaining product quality requires careful control at every stage of the production process. We use only the highest-quality raw materials, double-check the raw blocks before crushing, and conduct two rounds of magnetic separation at 8000 gauss to maintain purity.
Two rounds of fine screening ensure that the final product meets the specified grain size distribution. The use of ultrasonic vibrating screens in the final step guarantees that impurities are removed and the particles are consistent in size before packaging.
Consistent quality control ensures that our customers receive pink fused alumina that meets their requirements for grinding and abrasive applications. We strive to maintain the highest standards in every step, from raw material sourcing to final packaging.
Conclusion
The production process for pink fused alumina is intricate and involves several critical steps. From carefully selecting high-quality raw materials to precise crushing, shaping, screening, and refinement, every stage ensures that the final product meets stringent quality standards. By understanding this journey, you can appreciate the meticulous attention to detail required to produce a product that meets the high demands of grinding and abrasive tools.
Maintaining quality and consistency throughout the process is essential for delivering a final product that exceeds customer expectations.