The primary objective of sapphire grinding is to remove surface scratches, unevenness, and damage layers incurred during slicing, thus enhancing wafer flatness and reducing surface roughness to meet pre-polishing requirements. Industrial processing of sapphire surfaces from rough to mirror-smooth involves three sequential processes: rough grinding, fine grinding, and polishing. With each step, the total thickness variation and surface roughness of sapphire wafers gradually decrease.

Sapphire’s high hardness renders conventional abrasives ineffective for cutting. From a materials and grinding perspective, ideal materials for machining and grinding sapphire crystals include synthetic diamonds, boron carbide, and silicon dioxide. Synthetic diamonds, however, with their excessive hardness (Mohs hardness of 10), tend to scratch the surface during sapphire grinding, impairing transparency and proving costly. Silicon dioxide, with its lower hardness (Mohs hardness of 7), lacks sufficient grinding force, making sapphire grinding time-consuming and labor-intensive.Therefore, boron carbide abrasive (Mohs hardness of 9.3) emerges as an ideal material for machining and grinding sapphire crystals.
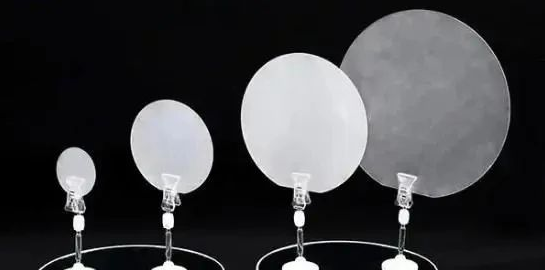
Boron carbide has been historically used as a coarse sand grinding material due to its high melting point, allowing it to be processed into simple shapes through high-temperature fusion powders for grinding, drilling, and polishing hard materials such as alloys and gemstones.
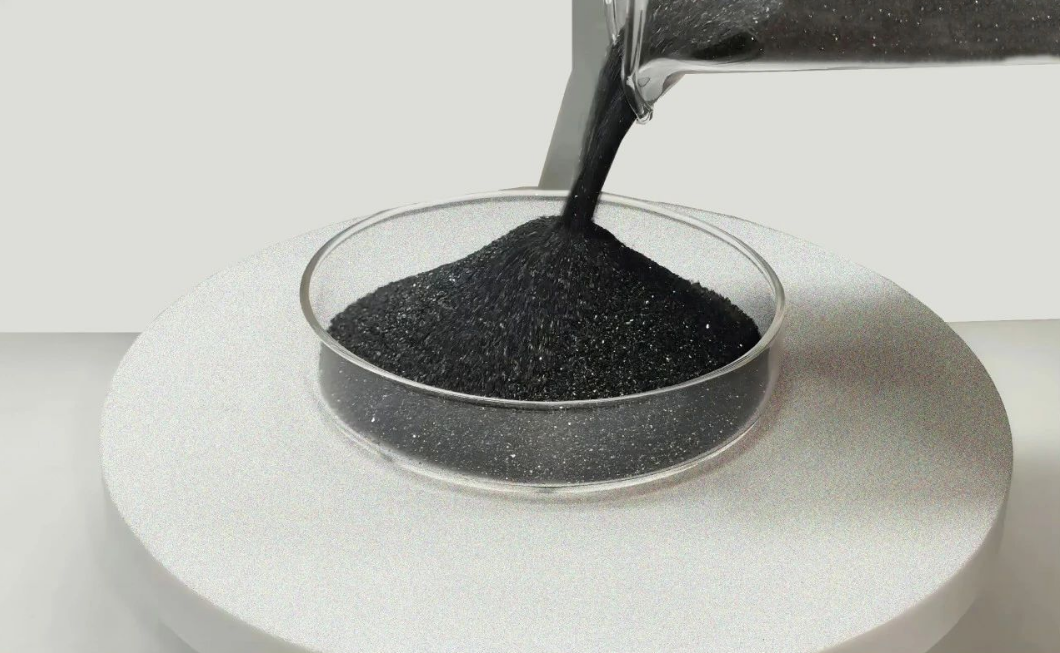
Boron carbide abrasive exhibits significant advantages over diamond abrasives in reducing the depth of subsurface damage in sapphire. Its prominent role extends beyond rough grinding, as composite particles with other abrasives show promising applications in enhancing the chemical-mechanical polishing surface quality and processing efficiency of sapphire.